After successfully setting up your aluminum extrusion plant, you should focus on churning out first-rate extrusion profiles. Supplying exceptional aluminum extrusion products means you can easily convert new clients to loyal clients, expanding your enterprise’s success. However, there is more to creating superior aluminum extrusion profiles than just having the right equipment. You also have to get several other factors you must get right. These factors are the following.
Factors that Affect Aluminum Extrusion Quality
1. Alloy Selection
Aluminum is often mixed with magnesium, manganese, copper, silicon, iron, and zinc to create different alloys like 2098 aluminum, 2124 aluminum, and 2195 aluminum. Each alloy has distinct properties that make it suitable for particular applications. Selecting the right alloy for the intended application of the extruded profiles means that the profiles you produce will have the strength and durability capabilities to handle the intended use.
2. Extrusion Temperature
Temperature adjustment is what makes the extrusion process possible. The aluminum billets have to be heated to a predetermined temperature to be extruded. Each aluminum alloy has specific heating temperature requirements. You must stick to the provided temperature parameters for each alloy during extrusion. Overheating the billets can make them brittle and diminish the quality of the extruded profiles.
3. Die Design
The die is what shapes the hot aluminum billets into the desired aluminum profiles during extrusion. Given its central role in the extrusion process, the die must be superbly designed with zero to minimal defects to generate high-quality extrusion profiles.
A defective die could introduce structural and tolerance problems to the extruded profiles. Moreover, it could make the extrusion process harder and longer, increasing profile production costs.
4. Lubrication
Friction is an ever-present challenge during the extrusion process of a press. The aluminum billets and the die have to be properly lubricated to minimize friction during the extrusion process. Additionally, lubrication prevents the hot aluminum extrusion billets from sticking to the die.
5. Speed of Extrusion
How fast the aluminum billets are extruded through the die will affect the quality of the extruded products. Fast extrusion speeds can cause the profiles to develop defects like poor dimensional accuracy. On the other hand, slow extrusion speeds mean that the extrusion process will take more time and be costlier.
6. Cooling Rate
The speed at which the hot extruded profiles are cooled can also influence their strength and other properties. Each extruded aluminum alloy should be subjected to its appropriate cooling parameters so it can maintain the desired properties. Ensure you have sufficient cooling beds to meet your production capacity.
7. Tongue Ratio
The tongue ratio of the aluminum profiles to be extruded often affects the extrusion performance. The higher the tongue ratio, the more time it will take for the aluminum profiles to be created, leading to higher operation costs. For optimal extrusion performance, it’s best to maintain the tongue profile of the profiles to be extruded below 2:1.
8. Parting Shot
The extrusion process has so many things that could go wrong, diminishing the quality of your extruded profiles. Employing qualified and experienced extrusion workers in your aluminum profiles production line is crucial in ensuring you end up with superb extrusion profiles.
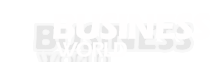