The Internet of Things (IoT) is all about connecting devices into networks that can work together. This is after a design transition from monolithic to segmented machines. That is, IoT is all about microprocessing and dividing big systems into different small systems. With this, it is very easy to manage the network, upgrade it, and maintain it.
Industrial Internet of Things (IIoT) has a significant function in manufacturing environments for several reasons. IoT analytics is one. Manufacturers must be aware of where they stand with their performance and what they lack, which is obtained through data. They can then make adjustments so that their business is optimized. This may even be able to be done automatically by making IIoT systems communicate with artificial intelligence.
Still, it’s always best to consider seriously how IIoT technologies can be applied to your company. It’s one of the highly effective methods to stay competitive as a business by putting together different technologies in innovative and new ways. It’s best to look at current manufacturing IoT trends in 2025 to have ideas about how precisely these technologies can help you.
Trend 1: Connectivity Technologies
Bandwidth is one of the biggest hurdles of IoT technology for manufacturing. How much data do all these devices in a network share at a specific time? The higher the volume of data that can be shared simultaneously, the more effective and faster such systems will become in other environments. Network speed is a crucial element in supporting real-time applications and edge computing with success. But if data doesn’t always have to be delivered as quickly as it can be, then extremely high bandwidth may not be needed. You must identify what your manufacturing company needs so that you can make the best decisions.
Wired IIoT Solutions
For the fastest and most responsive solutions, the best options are the wired IIoT connections for manufacturers who want to connect multiple IoT devices into one. They employ EtherCAT, Ethernet/IP, and Profinet protocols. USB cables have limited speed and range and, therefore, normally category cables are employed to lengthen their reach. For more distant deployments, fiber optic cables can be employed to link industrial factories miles away from one another.
Easier to use than wireless technology, wired solutions provide proven reliability and immunity to noise. The only downside of such connections is the physical aspect. Wiring can be space-hungry, environment-limited, and more installation-intensive. Wired connections also carry the added costs of cabling.
Wireless IIoT Solutions
For ease of use and flexibility of installation, wireless connections are much more effective. Even though wireless connections are themselves prone to inconsistency, this can be avoided based on the type of wireless connection used. There are a few technologies that are already in use and gaining popularity today in 2025 for manufacturing IIoT systems:
Bluetooth contains the frequency 2.4 GHz and commonly comes in the range of up to 10 meters (30 feet). Wi-Fi contains 5 GHz with up to around 57.9 meters (190 feet) possible indoors. Zigbee contains 2.4 GHz and possesses a range anywhere from 10 to 100 meters (32.8 to 328 feet).
Bluetooth Low Energy is more power-efficient than Zigbee and Wi-Fi. It is ideal for battery-powered and portable devices. Less data is transmitted at one time because of the power constraints. It is also a victim of interference in the 2.4 GHz band that both Bluetooth and regular Wi-Fi networks may be able to use, impacting how the devices function.
Zigbee is yet another type of connectivity that can act best with low-throughput sensors powered by a battery. It depends on the nodes that connect different paths. A hub coordinator will be needed in order to create more complexity for the system.
Wi-Fi also has a great deal of scope for factory machine sensors. Access points in 5 GHz permit such points to support high-speed connection to devices even at a distance of 190 feet. To offer maximum coverage, beacons can be installed in several locations on the factory floor. That can be the most perfect means of servicing cable-powered IIoT sensors that are mounted at fixed points.
Also, as there is no other communications cabling required, it is easy to install IIoT sensors that can be used to monitor machines. High-speed Wi-Fi connectivity is one of the finest solutions for industrial Internet of Things installations within factories in 2025. Today, almost every renowned IIoT platform has all these connectivity options that provide numerous advantages to its users.
Trend 2: Predictive Maintenance and Analytics
Industrial plant failures are very expensive. Companies can save millions of dollars with artificial intelligence-driven predictive maintenance. Industrial machine learning algorithms, though, need high-quality data regarding the machines they are assessing to operate. Industrial Internet of Things sensors can gather data from a set of machines. This data can be used to determine which machines have to be pre-scheduled for maintenance and when.
They are also able to make temperature, vibration, and power consumption readings on equipment in order to anticipate potential future points of failure.
Trend 3: Automated Quality Assurance
With Industrial Internet of Things networks, quality assurance monitoring can be automated and remote. This has the potential to enhance manufacturing business productivity and efficiency significantly. Real-time alerts can be triggered to enable quicker response to issues such as surprise machine breakdowns and other interferences. Real-time video link through IIoT devices also enables artificial intelligence initiatives such as automated visual inspection. This makes it possible for AI to identify defectives and sever them from the assembly line before they are shipped out. Visual inspection solutions based on AI would not be possible without IoT cameras and sensors to provide eyes and ears to the decision-making system.
Trend 4: Edge Computing
The most fascinating of all the trends in the Industrial Internet of Things technology space is edge computing. Several companies and industries have moved towards offloading processing from devices that are close to them to distant servers that do data processing on their behalf. While this reduces the amount of processing that needs to be performed by the local device like a cell phone or computer, it is costly in terms of bandwidth and time. Edge computing aims to keep as much processing as possible near the ‘edge’.
On factory floors where data is being produced, some devices on the local edge network of a factory are capable of processing the data without shipping it off to be processed elsewhere. Not only is this faster and more efficient, but it’s more secure as well. Because the data never actually leaves the factory, it can’t be intercepted or retrieved by a third party.
Forward-looking industrial businesses capitalize on emerging opportunities with the convergence of AI and edge computing as Edge AI. The Edge AI idea enables computation by AI near the user on the edge of the IoT network, rather than in a cloud. That delivers real-time intelligence to manufacturing processes, improves privacy, and improves security, all while minimizing costs and guaranteeing ongoing refinement of the factory operations. Recognizing this impact all software development services in the UK have now started to consider the importance of edge computing.
Trend 5: Location Tracking
Location tracking has a number of applications to manufacturing, and they all depend on Industrial Internet of Things technologies. Although GPS is widely known to be very effective in the majority of outdoor environments, indoor positioning systems and environments with GPS interference such as highly populated urban areas with skyscrapers can be difficult to handle. Solutions outdoors are generally in the realm of logistics, whereas solutions indoors are in the realm of manufacturing.
Real-time location systems (RTLS) enable wireless technologies like Wi-Fi, BLE beacons, UWB, and RFID. These can monitor where products are on the factory floor, which can be monitored from start to finish of the process of producing these products. These can not only assist in verifying the guarantee of quality but also generate additional data to capitalize on for digital twin applications.
Trend 6: Energy Optimization
You likely have walked into a black room at some point or another in your life, and the lights turn themselves on. It is not necessarily that they seem that way initially, but there is plenty we can learn from light switches that respond to motion. Their purpose is not so much to assist us in flipping the lights on. Their clandestine plan is to get to the point where if the room is not in use, then the lights turn off automatically. Where this connects with the Industrial Internet of Things is with energy optimization. We can optimize factory lights, but how do you optimize the energy draw of other machinery?
Energy optimization is done through various means, such as maximum precaution for temperature regulation mechanisms, factory equipment, etc. According to a study by EIA, in 2020, 33% of the overall energy consumption of the United States is attributed to the manufacturing industry. Energy optimization not only has the tendency to do less harm to the environment, but it can even produce tons of cost savings.
By leveraging IIoT energy optimization sensors to track the electrical condition and usage of equipment and machines within a factory, operators can automatically process-optimize as well as optimize energy use by different devices. That is only half the tale, however. It will require far more than IoT sensors and electricity data processing to make processes greener.
The Future of IoT in Manufacturing
Ultimately, the fate of the Industrial Internet of Things depends on several factors. Due to a shortage of chips that started last year and continues to haunt the market, there is only so much that companies can launch at lower prices. With sanctions against Russia tightening following the recent invasion of Ukraine, Bloomberg says the shortage will only worsen.
But that does not preclude the ability to purchase and install IIoT devices, and optimizing current systems as well. Amid disruption, innovation is very much necessary. While the chip shortage is dominating market growth, companies that can think their way through using resources already available and hardware on hand will be competitors for the remainder of the shortage. They will continue to thrive post-shortage as well, with even greater profit.
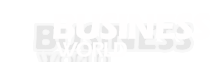