Steel, a sturdy and malleable alloy composed primarily of iron and carbon, has revolutionized various industries with its exceptional properties. From skyscrapers and bridges to automobiles and household appliances, steel serves as the backbone of modern infrastructure and technology. In this guide, we will uncover steel manufacturing, exploring the processes involved, different types of steel, and its vast applications.
What Does Mean By Steel?
Steel is an iron-carbon alloy containing less than 2% carbon by weight, making it stronger and more durable than pure iron. The carbon content influences its properties, such as hardness, ductility, and tensile strength.
Different Types of Steel
Steel comes in various forms, each tailored to specific applications and requirements. Understanding the different types of steel is crucial for manufacturers and designers to select the most suitable variant for their projects.
1. Carbon Steel
This widely-used type of steel contains a low to medium amount of carbon. It offers excellent strength and affordability, making it ideal for construction and manufacturing.
2. Stainless Steel
Known for its corrosion resistance, stainless steel is a popular choice in the food, medical, and chemical industries. It contains chromium, which forms a protective layer on the surface, preventing rust and corrosion.
3. Alloy Steel
Alloy steel is made by adding other elements, such as manganese, nickel, or chromium, to carbon steel. These additional elements enhance specific properties like hardness, strength, and heat resistance.
4. Tool Steel
Tool steel is designed to withstand high temperatures and provide exceptional hardness and wear resistance. It finds applications in manufacturing tools, molds, and dies.
Complete Process of Steel Manufacturing
The production of steel involves a complex series of steps, each playing a crucial role in creating a high-quality, reliable material.
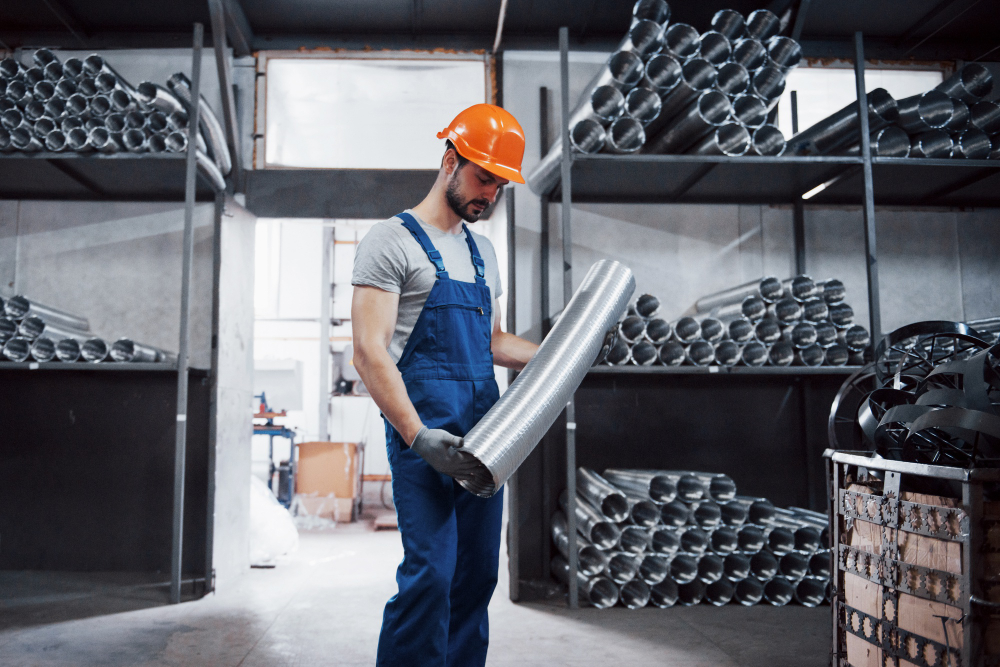
1. Iron making
In the first stage of steel production, iron ore is extracted from the earth through mining. The ore is then processed in a blast furnace, where it is heated to extreme temperatures along with coke (a form of coal) and limestone. The intense heat causes the iron ore to undergo chemical reactions, resulting in the formation of molten iron.
2. Steelmaking
Once the molten iron is obtained, it is further processed to convert it into steel. This step involves removing impurities such as carbon, sulfur, and phosphorus from the molten iron. One common method for steelmaking is the basic oxygen furnace (BOF) process, where a lance is used to inject oxygen into the molten iron, oxidizing the impurities and reducing their content.
3. Casting
After steelmaking, the molten steel is cast into various shapes to meet the specific requirements of different industries. One method of casting is continuous casting, where the liquid steel is poured into a water-cooled mold. As the steel cools and solidifies, it is continuously drawn out in the desired shape, such as slabs, blooms, or billets.
4. Forming
Forming is the process of shaping the steel into its final product. This can be done through various methods, including rolling, forging, extrusion, and drawing. Rolling, the most common forming technique involves passing the steel through a series of rollers to reduce its thickness and shape it into sheets, plates, or structural sections.
5. Heat Treatment
Heat treatment is a critical step in steel manufacturing that enhances its mechanical properties. This process involves heating the steel to a specific temperature and then rapidly cooling it to achieve desired characteristics such as increased strength, hardness, or ductility. Common heat treatment methods include annealing, quenching, tempering, and case hardening.
6. Finishing
The final in the steel manufacturing process is finishing, which involves surface treatments to improve appearance, durability, and corrosion resistance. Finishing techniques include cleaning, coating, painting, galvanizing, and polishing. These processes provide a protective layer to the steel, ensuring its longevity and enhancing its aesthetic appeal.
Various Applications of Steel
1. Construction
Steel is widely used in the construction industry for building structures, including skyscrapers, bridges, and stadiums. Its high strength-to-weight ratio allows for efficient and durable construction, ensuring the safety and stability of the built environment.
2. Automotive
Steel plays a vital role in the automotive industry, where it is used in the production of car bodies, chassis, and engine components. Its strength, crash resistance, and formability make it an ideal material for ensuring vehicle safety and performance.
3. Manufacturing and Machinery
Steel is a primary material in manufacturing processes, serving as a key component in machinery, equipment, and tools. Its durability, reliability, and machinability make it indispensable in industries such as aerospace, energy, and machinery manufacturing.
4. Energy and Infrastructure
Steel is essential for the production, transportation, and storage of energy. It is used in pipelines, oil rigs, wind turbines, and power transmission towers. steel is crucial for infrastructure development, including railways, airports, and ports.
Conclusion
Steel is a versatile and essential material that is an important material in numerous industries, ranging from construction to automotive manufacturing. Its durability, strength, and ability to be molded into various shapes make it a preferred choice for engineers and designers worldwide.
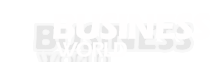